
However, at reduced loads with constant field current, the motor will operate at leading power factor.

The unity power factor machine does not provide any leading current at rated load. At zero load, with rated field current, the available leading reactive kVA is approximately 80% of the motor-rated kVA. This leading reactive kVA increases as load decreases. At 80% power factor, 60% of the motor-rated kVA is available to be delivered to the system as reactive kVA for improving the system power factor. Standard synchronous motors are available rated either 100% or 80% leading power factor. One interesting characteristic of synchronous motors is their ability to provide power factor correction for the electrical system. In fact, at the lowest speeds, larger sizes and highest hp/rpm ratios may be the only choice. For example, applications of several hp per rpm often offer a distinct advantage of the synchronous over the induction motor. However, the rule can aid in the selection of the motor type by giving some insight as to when the synchronous motor might be chosen. This, of course, was only an approximation and tended to favor the selection of a synchronous motor it would be considered too severe by current standards. Typical applications of this type are geared, high-speed (above 3600 rpm) centrifugal compressor drives of several thousand horsepower.Ī rule of thumb that was used in the past for constant speed applications was to consider the selection of a synchronous motor where the application horsepower was larger than the speed. They are also useful on many large, high-speed drives. They are the obvious choice to drive large, low-speed reciprocating compressors and similar equipment requiring motor speeds below 600 rpm. Synchronous motors have definite advantages in some applications. E., in Compressors (Third Edition), 2005 Synchronous Motors These disadvantages, coupled with the requirement for an independent starting mode, make synchronous motors much less common than induction ones.

supply is a necessary feature of the rotor excitation. Synchronous motors, however, are generally more expensive and a d.c. The advantages of the synchronous motor are the ease with which the power factor can be controlled and the constant rotational speed of the machine, irrespective of the applied load. The machine is run up to speed as an induction motor and is then pulled into synchronism to operate as a synchronous motor. A second method uses a wound rotor similar to a slip-ring induction motor. The rotating magnetic flux induces currents in these ‘grids’ and the machine accelerates as if it were a cage-type induction motor (see Section 2.2.21).
#POSSIBL VALUES OF SYNCHRONOUS SPEED NS SERIES#
One method utilizes a series of short-circuited copper bars inserted through the outer extremities of the salient poles. It is evident from equation (2.81) that synchronous motors have no starting torque and the rotor must be run up to synchronous speed by some alternative means. Where T max is the maximum rated torque and δ is the load angle. In this case, a high starting torque can be developed by using the information of the rotor initial position.
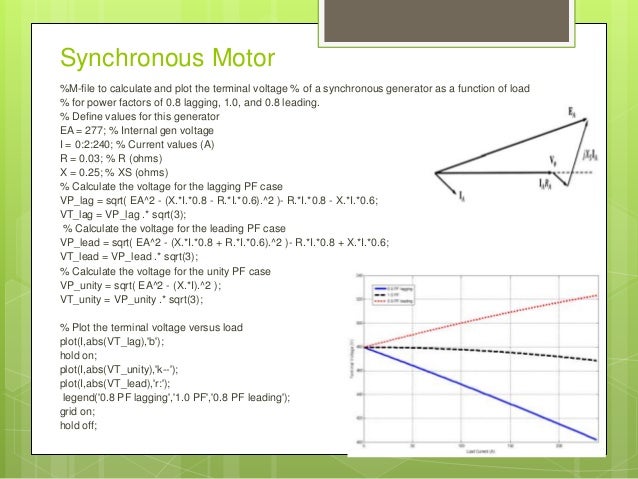
If the speed of the motor is increased or decreased from the synchronous speed, then a current will be induced in the damper winding and will develop a torque to oppose the change in speed.Īs for the starting method of PMSMs used in variable speed drives, we can start the motor slowly at a reduced frequency by using a PWM inverter. In addition, the damper winding has another function to help keeping the synchronous motor in synchronism. When the synchronous motor is starting, the torque will be produced by the induced current in the damping winding, so it can start as an induction motor. In this case, the rotor has a special damping winding for the purpose of starting, which is similar to the squirrel-cage arrangements of an induction motor. A second method is to start the synchronous motor as an induction motor. As a simple method, a separate motor is used to drive the rotor to run close to the synchronous speed. There are some techniques employed to start a synchronous motor. Once the rotor reaches a speed close to the synchronous speed (>95%) through some starting means, the field winding will be excited, so the motor locks into synchronization. Therefore we need some means for starting synchronous motors.
